Molding Precision: The Cornerstone of Metal Fabrication
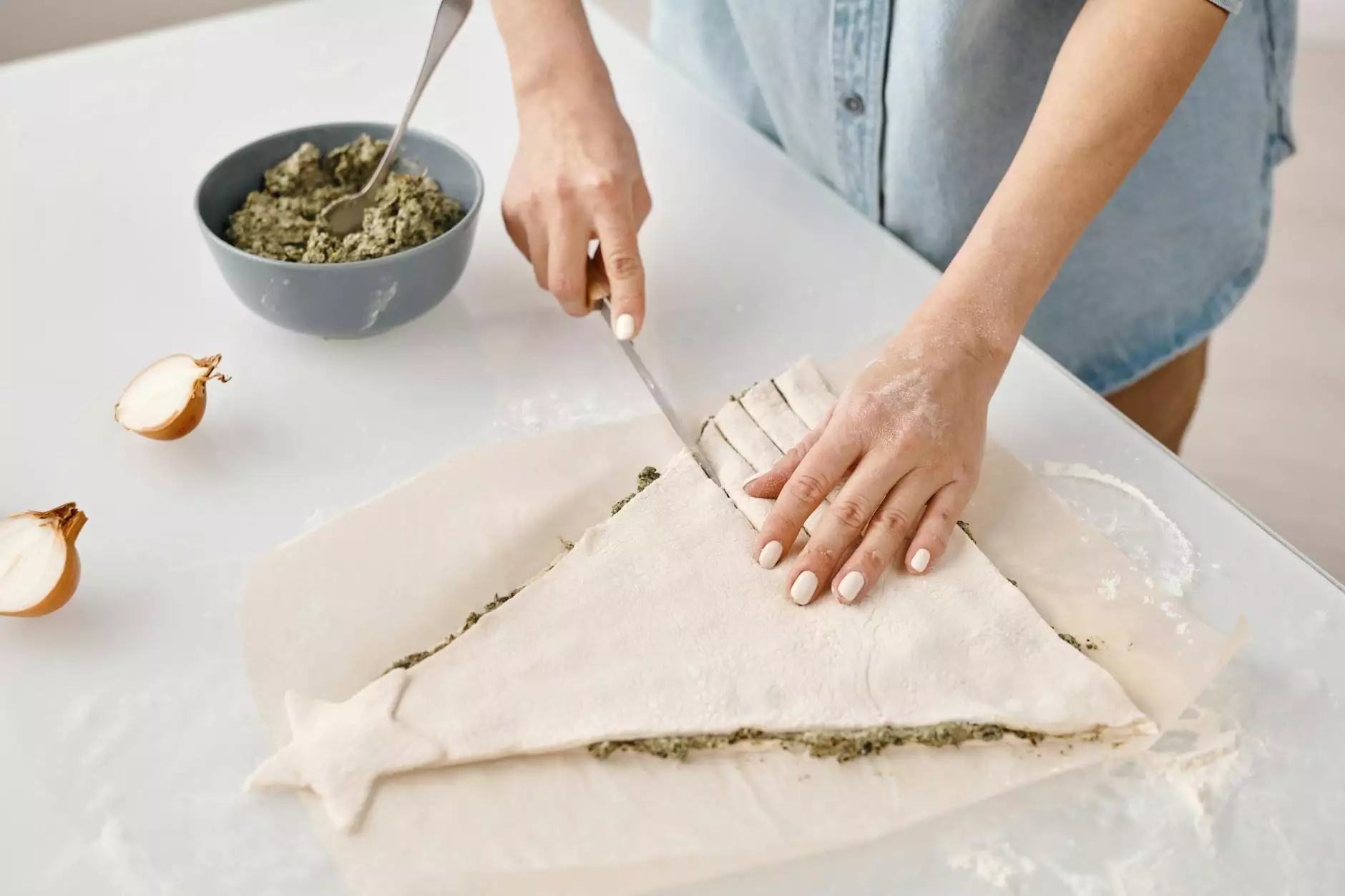
In the realm of metal fabrication, one term that resonates with significance is "molding precision." This phrase encapsulates the essence of accuracy and meticulousness that dictates the quality and performance of fabricated components. The process of molding in metal fabrication encompasses a variety of techniques and applications, each of which requires a keen eye for detail and stringent adherence to specifications to yield products that meet the highest standards.
Understanding Molding Precision
Molding precision refers to the exactness with which raw materials are shaped and formed into specific geometries through various techniques, including but not limited to casting, stamping, and machining. Precision in these operations is crucial as it directly impacts not only the dimensionality of the fabricated parts but also their functionality in real-world applications.
The Importance of Molding Precision in Metal Fabrication
In the competitive landscape of metal fabrication, molding precision is not just a desirable trait; it is a fundamental requirement. Here are several reasons why:
- Quality Assurance: Parts that are molded with precision conform to the required specifications, reducing the likelihood of defects and ensuring a high standard of quality in production.
- Cost Efficiency: Precision reduces material wastage and minimizes the need for rework, which can significantly decrease production costs and improve overall efficiency.
- Enhanced Performance: Components that are manufactured with meticulous attention to detail often perform better under stress, are more reliable, and exhibit longer lifespans.
- Customer Satisfaction: Delivering high-quality precision-engineered products meets and exceeds customer expectations, fostering loyalty and potentially increasing market share.
Key Techniques for Achieving Molding Precision
To achieve molding precision in metal fabrication, various techniques and practices are employed. Below are some of the most common:
1. CNC Machining
Computer Numerical Control (CNC) machining is a technology that utilizes computer systems to control machine tools. This method allows for highly precise cuts and shapes to be made in metal components. Key features include:
- Automation: Reduces human error.
- Complex Geometries: Capable of producing intricate shapes that traditional methods may not handle.
- Consistency: Able to replicate exact specifications indefinitely.
2. Injection Molding
Injection molding is a manufacturing process for producing parts by injecting material into a mold. Precision in this method comes from:
- Controlled Conditions: Ensuring temperature and pressure are regulated maintains material properties.
- Custom Molds: Using tailored molds that fit exact dimensions helps in achieving desired results.
3. 3D Printing
In recent years, 3D printing has emerged as a revolutionary technique in metal fabrication. It permits:
- Rapid Prototyping: Fast production of prototypes to test designs for accuracy.
- Complex Internal Structures: The ability to produce complex parts that were previously impossible to manufacture.
4. Precision Casting
Precision casting is another method that enhances molding precision by allowing for intricate designs with minimal finishing required. It involves:
- Investment Casting: Producing molds from a wax pattern, leading to high-fidelity part replicas.
- Sand Casting: Utilizing sand molds for bulk production while retaining fine details.
Challenges in Achieving Molding Precision
While the methods mentioned above can significantly enhance precision, several challenges pose threats to achieving optimal results:
Material Variability
Different materials behave differently under various processing conditions. Understanding material properties is essential for accurate molding.
Tooling Maintenance
Maintaining tools in top condition is vital; worn-out tools can lead to inaccuracies in molding.
Environmental Factors
Temperature, humidity, and other environmental factors can affect the molding process. Consistent environmental controls are necessary to mitigate these effects.
Ensuring Molding Precision in Your Operation
For businesses aiming to elevate their metal fabrication processes, incorporating the following best practices can enhance molding precision:
- Regular Training: Investing in employee training ensures that workers are versed in the latest techniques and technologies.
- Quality Control Systems: Implementing rigorous quality control measures throughout the production process minimizes errors.
- Advanced Software Tools: Utilizing advanced software for design and modeling aids in achieving precise specifications before manufacturing begins.
- Collaboration with Experts: Partnering with specialized firms or consultants can help businesses refine their processes and achieve better results.
Future Trends in Molding Precision
As technology continues to evolve, the future of molding precision in metal fabrication looks promising. Here are a few emerging trends to watch:
Integration of AI and Machine Learning
Artificial Intelligence (AI) and machine learning systems are beginning to take hold in manufacturing. These technologies can predict outcomes based on historical data and automatically adjust processes to improve precision.
Smart Manufacturing
The Internet of Things (IoT) will play a crucial role in manufacturing, with machines communicating data in real-time to optimize production processes for greater accuracy.
Sustainable Practices
As industries move towards sustainability, precision methods will evolve to minimize waste and energy consumption while maintaining molding precision.
Conclusion: The Role of Molding Precision in Metal Fabrication's Future
In conclusion, molding precision stands as a foundational element in the field of metal fabrication. It encompasses a vast array of techniques and methodologies that ensure products meet demanding specifications and offer peak performance. As the industry progresses, embracing advanced technologies and continuous improvement practices will further enhance the ability to achieve molding precision. For metal fabricators, the pursuit of precision is not merely an operational goal but a pathway to innovation, and success in a competitive landscape.
For businesses in the metal fabrication segment, fostering a culture of precision within their operational framework is critical. By understanding and implementing the principles outlined in this article, companies can not only improve their products but also solidify their reputation as leaders in the industry.
To learn more about how to achieve molding precision and explore various metal fabrication solutions, visit Deep Mould.