Understanding OEM Machining Lathe Parts Factory
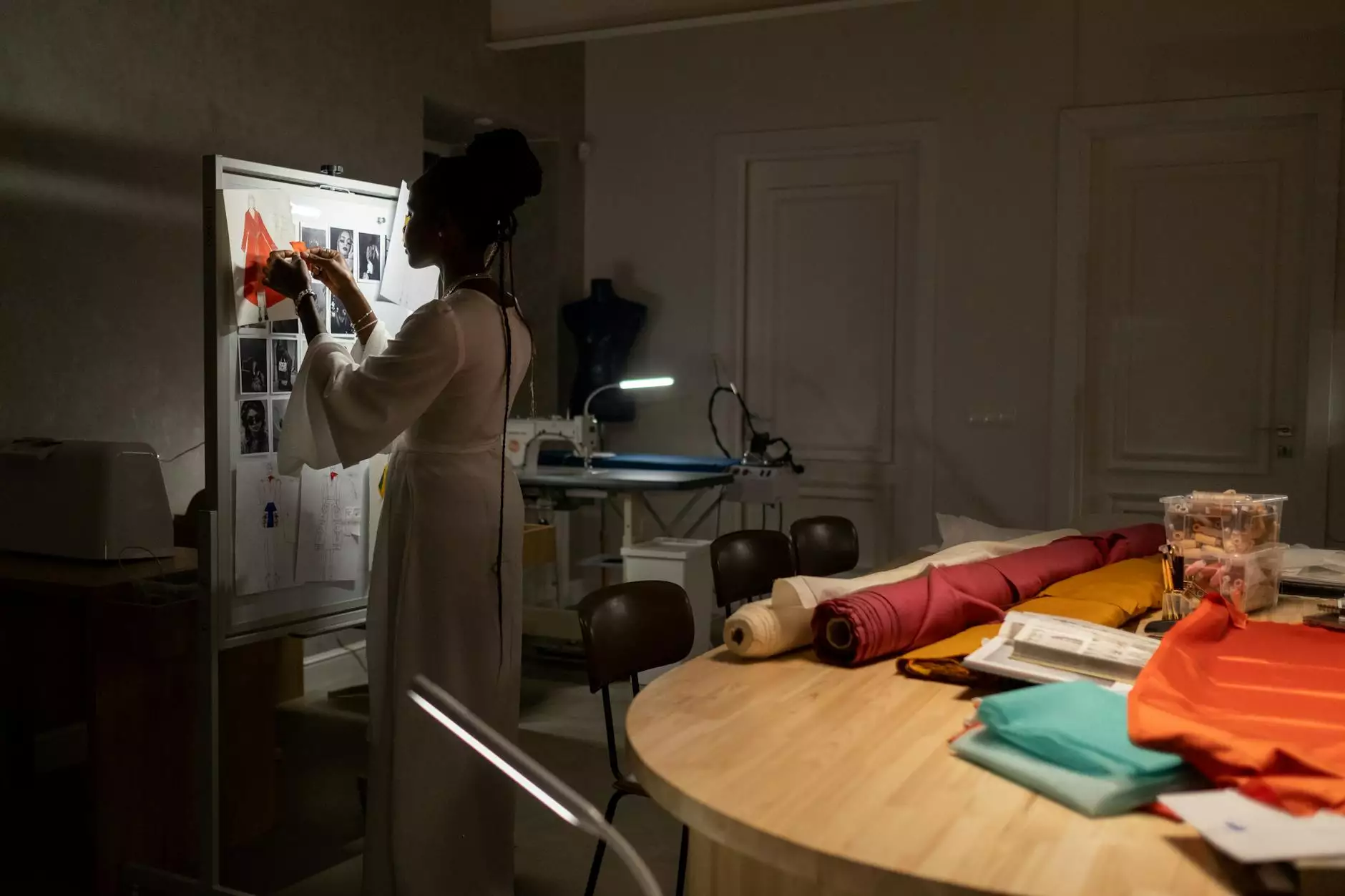
The world of manufacturing and engineering is continually evolving, and one area that has seen significant advancements is OEM machining lathe parts factory. This article delves into the essential facets of OEM machining, the unparalleled advantages offered by top-tier factories, and why companies like DeepMould.net stand out in the metal fabricators sector.
What is OEM Machining?
OEM stands for Original Equipment Manufacturer. In the context of machining, it refers to companies that produce parts intended for use in another company's products. These parts are crafted to precise specifications to ensure compatibility and quality. The process of OEM machining involves a combination of cutting-edge technology, skilled labor, and meticulous attention to detail.
The Role of Lathe Parts in Manufacturing
Lathe parts play a crucial role in various manufacturing processes. They are typically used for shaping, cutting, and finishing materials, making them indispensable in industries ranging from aerospace to automotive. Some of the core functionalities of lathe parts include:
- Precision Cutting: Lathe parts are designed to make precise cuts, ensuring that the final products meet exact specifications.
- Versatility: These parts can be used with different materials, including metals, plastics, and composites, enhancing their utility across various industries.
- High Efficiency: Lathes, when paired with quality parts, can operate at high speeds while maintaining high accuracy, significantly boosting productivity.
DeepMould: Your Trusted Partner in OEM Machining
DeepMould is a leader in the field of metal fabrication and OEM machining. With a commitment to quality and customer satisfaction, we have established ourselves as a reliable partner for businesses in need of precision components. Let’s explore some of the reasons why DeepMould is the go-to choice for OEM machining lathe parts:
1. Advanced Technology and Equipment
At DeepMould, we invest in the latest machining technology to guarantee the production of high-quality parts. Our sophisticated machines are equipped to handle complex designs with precision, resulting in consistent and reliable outcomes.
2. Skilled Workforce
Our team of experienced machinists and engineers is dedicated to excellence. They possess in-depth knowledge of machining processes and quality control, which ensures that every lathe part produced meets the highest standards.
3. Comprehensive Quality Control
Quality assurance is the backbone of our manufacturing process. Each part undergoes rigorous inspection and testing, including:
- Dimensional accuracy checks
- Material quality assessments
- Performance testing under various conditions
This comprehensive approach ensures that only the best components reach our clients, enhancing their final products' overall quality.
Benefits of Partnering with an OEM Machining Lathe Parts Factory
Choosing to work with an OEM machining lathe parts factory, especially one as reputable as DeepMould, provides several advantages:
1. Cost-Effectiveness
By sourcing parts from a specialized factory, businesses can reduce their overall production costs. Our optimized processes ensure that each lathe part is manufactured efficiently without compromising quality, allowing our clients to maintain competitive pricing.
2. Customization Options
One of the primary benefits of OEM machining is the ability to customize parts according to specific needs. At DeepMould, we collaborate closely with our clients to design and manufacture lathe parts tailored to their unique applications.
3. Reliability and Consistency
When businesses depend on our OEM machining services, they benefit from the reliability and consistency in the quality of their components. With our strict quality control measures, customers can rest assured that they will receive parts that perform as expected every time.
Industries Benefiting from OEM Machining Lathe Parts
Numerous industries rely heavily on OEM machining lathe parts. Here are some of the major sectors that benefit:
- Aerospace: Utilizing lightweight and durable lathe components for aircraft assemblies.
- Automotive: Manufacturing engine components and precision parts for fuel systems.
- Medical Devices: Producing intricate parts that meet stringent FDA regulations.
- Electronics: Creating precision housings and connectors for electronic devices.
- Industrial Equipment: Fabricating parts for heavy machinery that require robust durability.
The Future of OEM Machining in the Manufacturing Industry
The landscape of OEM machining is undergoing rapid transformation, influenced by technological advancements and changing market demands. Some trends shaping the future of the industry include:
1. Automation and Robotics
With the rise of automation, many OEM machining processes are becoming more efficient. Integrating robotic systems in machining can enhance precision and reduce production times, paving the way for increased productivity.
2. Advanced Materials
The development of new materials is creating opportunities for OEM manufacturers to expand their offerings. High-performance composites and lightweight alloys are being increasingly utilized, requiring sophisticated machining techniques.
3. Sustainability Trends
Environmental considerations are at the forefront of modern manufacturing. OEM machining factories, including DeepMould, are implementing sustainable practices, such as minimizing waste and utilizing eco-friendly materials.
Conclusion
Understanding the intricacies of the OEM machining lathe parts factory environment is essential for businesses aiming to excel in today’s competitive market. Whether you are in aerospace, automotive, electronics, or other industries requiring precision parts, partnering with a reliable manufacturer like DeepMould ensures that you receive the quality and performance necessary for your operations.
As industries evolve and technology progresses, companies must stay ahead by leveraging the advantages of OEM machining. With the right partner, like DeepMould, businesses can look forward to enhanced efficiency, reduced costs, and increased product quality.
For more information about how DeepMould can support your OEM machining needs, please visit DeepMould.net.