Leading Silicone Injection Molding Manufacturers: Innovations in Electronics & Medical Supplies
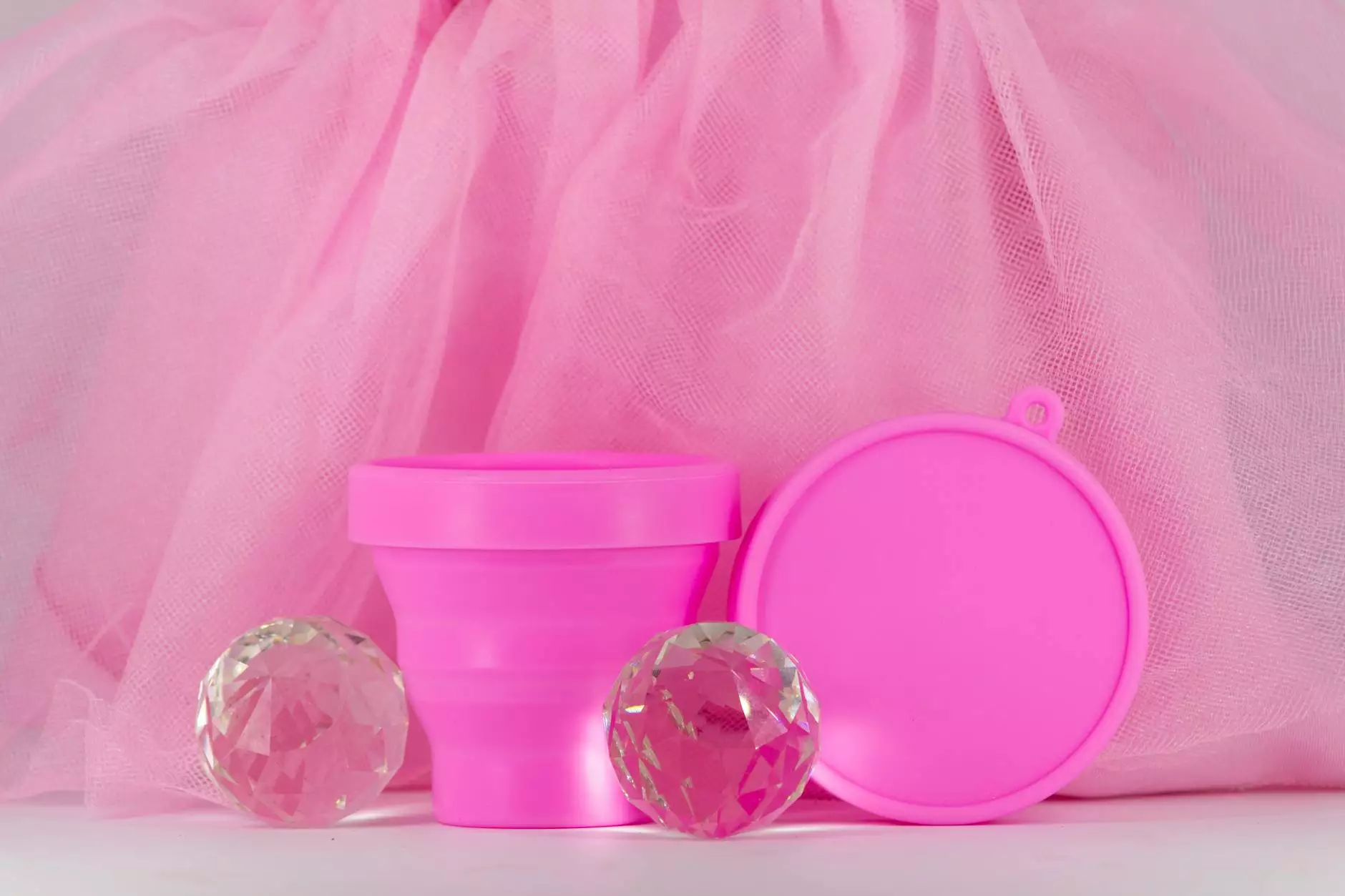
The manufacturing landscape is evolving rapidly, and within this change, silicone injection molding manufacturers stand at the forefront of innovation, particularly in the realms of electronics and medical supplies. This article explores the intricacies of silicone injection molding, its importance in various industries, and how leading manufacturers are driving technological advancements.
Understanding Silicone Injection Molding
Silicone injection molding is a manufacturing process that involves the creation of silicone products by injecting heated silicone into a mold. This method is favored for its ability to produce complex shapes with superior precision and consistency. The properties of silicone, such as its flexibility, durability, and resistance to temperature, make it an ideal material for a variety of applications.
Key Benefits of Silicone Injection Molding
- Versatility: Silicone can be molded into numerous shapes, making it suitable for various applications across different sectors.
- Durability: Silicone products are known for their longevity, resisting wear and tear more effectively than alternative materials.
- Temperature Resistance: Silicone maintains its properties across a wide range of temperatures, making it suitable for high-performance environments.
- Biocompatibility: Particularly important in the medical sector, silicone is non-toxic and compatible with human tissue, ensuring safety for medical applications.
- Environmental Benefits: Silicone is an eco-friendly material, as it can be produced with sustainable practices and is recyclable.
The Role of Silicone Injection Molding in Electronics
In the electronics industry, the demands for precision, reliability, and innovation are ever-increasing. Silicone injection molding plays a critical role by providing components that meet these high standards. Products such as keypads, connectors, and insulating materials are essential for the functionality of electronic devices.
Applications in Electronics
- Keypads and Seals: Silicone keypads provide not only durability but also tactile feedback, enhancing user interaction with devices.
- Insulation: Silicone's excellent dielectric properties make it a prime choice for insulating components within electronic devices.
- Enclosures: Flexible silicone enclosures protect sensitive electronics from moisture and dust.
- Adhesives: Silicone-based adhesives offer strong bonding capabilities while maintaining flexibility for dynamic applications.
Advancements in Medical Supplies Using Silicone Injection Molding
The medical industry relies heavily on silicone injection molding for producing high-quality medical devices and supplies. The biocompatibility of silicone makes it a preferred choice for products that come into direct contact with patients.
Applications in Medical Supplies
- Medical Tubing: Silicone tubing is widely used in various medical applications due to its chemical resistance and durability.
- Implants: Many implants utilize silicone due to its compatibility with human tissue, minimizing the risk of rejection.
- Valves and Seals: Silicone valves are essential for controlling fluid flow in various medical devices.
- Consumer Medical Devices: Devices such as nebulizers and insulin delivery systems often use silicone components for their reliability and safety.
The Leading Silicone Injection Molding Manufacturers
Now that we have explored the significance of silicone injection molding in the electronics and medical sectors, let's take a closer look at some of the leading silicone injection molding manufacturers that are making strides in these industries.
Nolato: Setting the Standard
Nolato, a name synonymous with quality in silicone injection molding, is known for its innovative solutions in electronics and medical supplies. With a robust R&D department, Nolato continues to advance the technology behind silicone applications, ensuring they meet the highest industry standards.
Other Notable Manufacturers
- Wacker Chemie AG: A global leader in silicone production, Wacker Chemie invests heavily in research to enhance silicone molding technologies.
- Shin-Etsu Chemical Co., Ltd: Well-known for their silicone polymers, Shin-Etsu focuses on providing tailor-made solutions for diverse industries.
- Momentive Performance Materials: This company specializes in advanced silicone products and is a significant player in the medical sector.
- Dow Corning: With an extensive range of silicone products, Dow Corning implements cutting-edge technologies to ensure quality and performance.
Challenges Faced by Silicone Injection Molding Manufacturers
While the benefits of silicone injection molding are considerable, manufacturers also face challenges that can impact their efficiency and competitiveness.
Common Challenges
- Material Costs: The price of raw silicone material can fluctuate, affecting production costs.
- Complexity of Designs: As customer demands for complex designs increase, manufacturers must invest in advanced tooling and precise engineering.
- Regulatory Compliance: Especially in the medical field, manufacturers must ensure compliance with stringent regulations, which can be resource-intensive.
- Supply Chain Disruptions: Global supply chain issues can impact the availability of materials and lead to delays in production.
The Future of Silicone Injection Molding
The future of silicone injection molding looks promising, with technological advancements paving the way for new innovations. The following trends are shaping the next generation of silicone products:
Trending Innovations
- Automation and Robotics: Increased use of automation in the production process is leading to greater efficiency and reduced labor costs.
- 3D Printing Integration: Combining 3D printing technology with silicone molding allows for more rapid prototyping and customization.
- Smart Materials: The development of responsive materials that adapt based on environmental stimuli is a growing area of research.
- Sustainability Initiatives: Manufacturers are focusing on reducing waste and using sustainable practices in their production processes to address environmental concerns.
Choosing the Right Silicone Injection Molding Manufacturer
When selecting a silicone injection molding manufacturer, it's imperative to consider several key factors to ensure you partner with the best in the industry.
Factors to Consider
- Experience and Expertise: Look for manufacturers with a proven track record in your specific industry.
- Technology and Equipment: Ensure the manufacturer uses state-of-the-art technology to deliver high-quality products.
- Quality Assurance Processes: A robust quality control system is essential for ensuring product reliability.
- Flexibility in Production: The ability to adapt to changing demands and customization requests is crucial.
- Customer Support: Strong support services can greatly enhance the partnership and project outcomes.
Conclusion: The Impact of Silicone Injection Molding Manufacturers
In conclusion, silicone injection molding manufacturers play a critical role in advancing technology in the fields of electronics and medical supplies. By continuously innovating and adapting to industry challenges, these manufacturers not only create high-quality products but also drive the entire manufacturing landscape forward.
As the industry evolves, it is essential for companies to collaborate with leaders like Nolato to harness the benefits of silicone injection molding, paving the way for innovations that improve functionality, safety, and user experience across various sectors.