The Future of Precision Injection Mould Plastics in Business
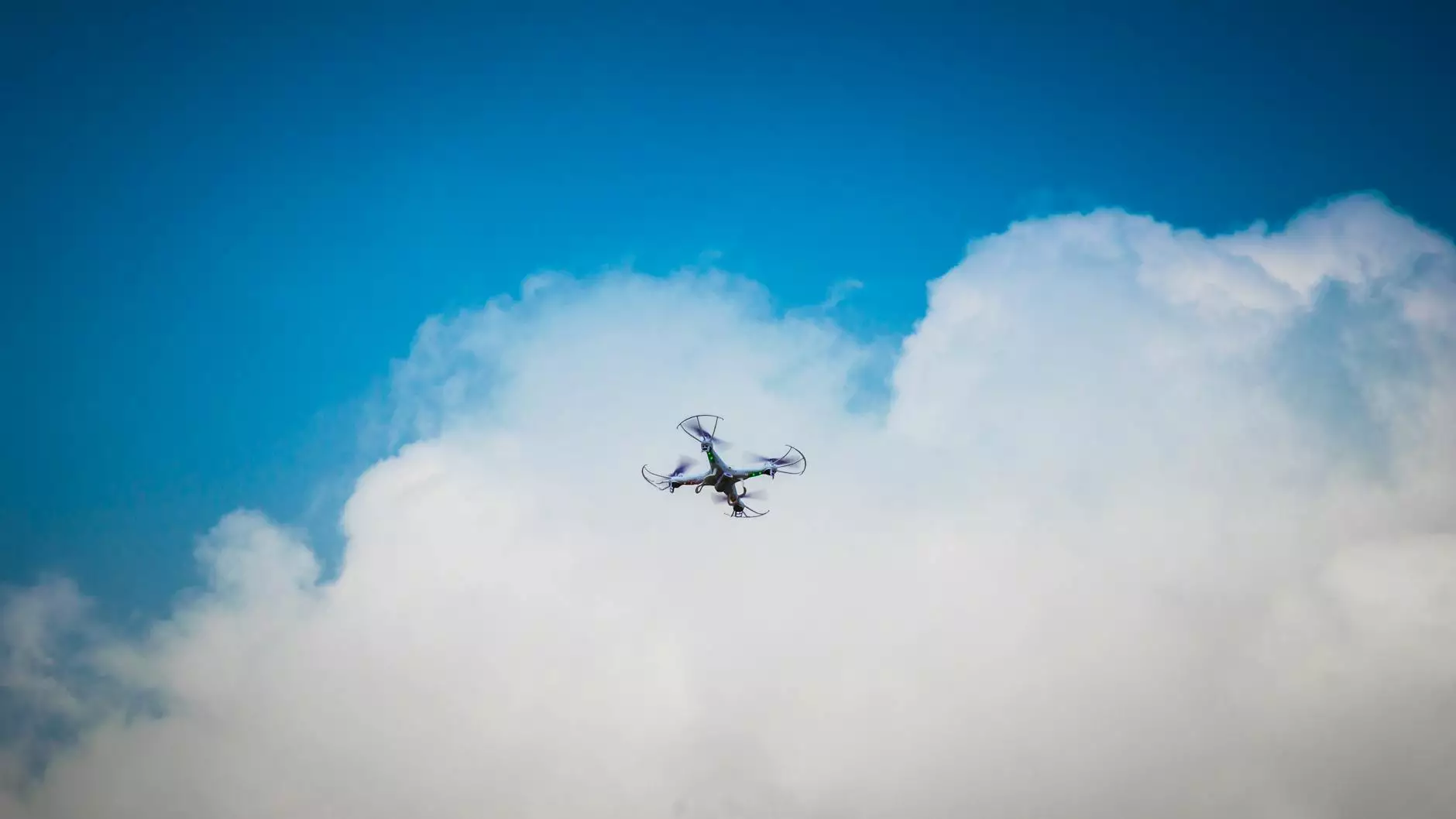
The world of manufacturing is evolving rapidly, and at the forefront of this transformation is the concept of precision injection mould plastics. This method has revolutionized how businesses think about production, allowing for higher efficiency, quality, and versatility. In this article, we will delve into the vast benefits and applications of precision injection mould plastics, particularly in the context of industries like Metal Fabricators.
Understanding Precision Injection Mould Plastics
Precision injection mould plastics involve a manufacturing process where molten plastic is injected into a mould cavity to create parts with intricate designs and dimensions that require a high level of accuracy. This process is beneficial in creating both simple and complex shapes, which have critical applications across various industries.
The Process of Precision Injection Moulding
The precision injection moulding process typically involves several key steps:
- Material Selection: The right type of plastic is chosen based on the desired properties of the final product.
- Mould Design: Engineers design a mould that meets the specifications of the product while considering factors like cooling time and material flow.
- Injection: The selected plastic is heated and injected under pressure into the mould.
- Cooling: The plastic is allowed to cool and solidify in the mould, ensuring the precision of the final product.
- Demoulding: Once the part has cooled, it is removed from the mould and undergoes any necessary finishing processes.
Advantages of Precision Injection Mould Plastics
The advantages of using precision injection mould plastics are manifold. Here are some key benefits:
- Cost-Effectiveness: This process reduces waste and can produce large quantities of parts at a lower cost compared to traditional manufacturing methods.
- High Precision: Parts are created with extremely tight tolerances, which is crucial for applications that require detailed specifications.
- Material Versatility: A wide variety of plastics can be used, providing manufacturers with options suited for different applications.
- Complex Geometries: This technique allows for intricate designs that are difficult or impossible to achieve with other manufacturing processes.
- Rapid Production: The speed of the injection moulding process ensures that parts can be produced quickly to meet market demands.
Applications of Precision Injection Mould Plastics
Precision injection mould plastics find applications in numerous sectors, including:
Automotive Industry
In automotive manufacturing, precision injection mould plastics are used to create components such as dashboards, interior trim pieces, and various housings. The lightweight nature of these plastics contributes to fuel efficiency and design flexibility.
Medical Devices
Medical devices require stringent quality and precision standards. Injection moulded plastics are used to manufacture items such as syringes, surgical instruments, and housings for electronic devices. The ability to create sterilizable components is essential in this sector.
Consumer Goods
From toys to kitchen appliances, the consumer goods sector benefits from the versatility of precision injection mould plastics. High-quality finishes and colors can be achieved, enhancing the visual appeal of the products.
The Role of Metal Fabricators in Precision Injection Moulding
While precision injection mould plastics primarily deals with plastics, metal fabricators play a crucial role in the process. They provide the high-quality moulds necessary for injection moulding, crafted from metals that can withstand the pressures of injection and maintain precision during the production process.
Metal fabricators help in:
- Mould Creation: Designing and manufacturing the moulds that shape the plastic into its final form.
- Maintenance and Repair: Ensuring that existing moulds are maintained for longevity and can be repaired as needed to keep production efficient.
- Technical Expertise: Offering insights and engineering support for complex mould designs to enhance production quality.
Environmental Considerations in Precision Injection Mould Plastics
The manufacturing industry is increasingly focused on sustainability. Precision injection mould plastics can contribute to environmentally friendly practices in various ways:
- Material Efficiency: The injection process minimizes waste, and advancements in technology are leading to the use of recycled plastics.
- Durability: Products made with precision moulding often have longer lifespans, which reduces the frequency of production and disposal.
- Energy Efficiency: Modern injection moulding machines are designed to use less energy, further reducing the environmental footprint of the production process.
Future Trends in Precision Injection Mould Plastics
As technology continues to advance, the future of precision injection mould plastics is bright. Here are several trends that are shaping its evolution:
3D Printing Integration
The integration of 3D printing technology with injection moulding offers new possibilities for rapid prototyping and low-volume production runs. This can significantly reduce lead times and costs.
Advanced Materials
There is a growing trend toward exploring advanced materials, including biodegradable plastics and composites that enhance the properties of injection moulded products.
Smart Manufacturing
Industry 4.0 technologies, including IoT (Internet of Things), are finding their way into injection moulding. This allows for better monitoring and optimization of the moulding process, leading to improved efficiency and quality control.
Conclusion
In the ever-evolving landscape of manufacturing, precision injection mould plastics stand out as a transformative technology that is changing the way businesses operate. With its numerous advantages, extensive applications, and ongoing innovation, this method continues to drive efficiency and competitiveness across various industries. The role of metal fabricators in providing the necessary moulds cannot be overstated, highlighting the importance of collaboration in manufacturing.
As we move forward, embracing the trends and advancements in precision injection mould plastics will be vital for businesses aiming to maintain an edge in the market. The future is undoubtedly bright, and those who adapt and innovate will thrive in this dynamic environment.