The Future of Construction: Embracing Prefabricated Building Solutions
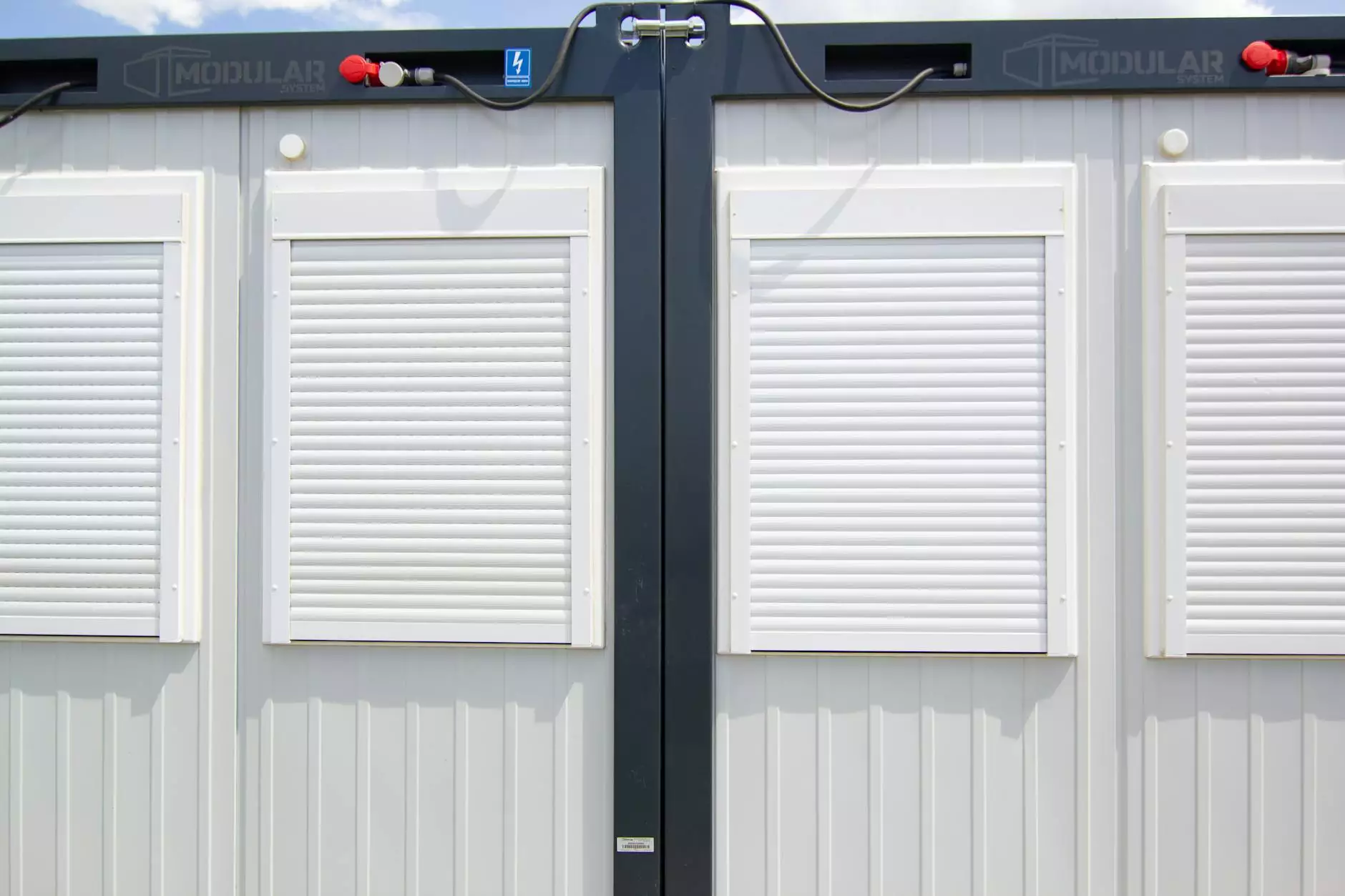
In recent years, the building and construction industry has witnessed a significant transformation. Among the innovations reshaping this sector is the concept of prefabricated building. This method of construction, which involves assembling buildings from factory-made modules, has garnered a lot of attention for its efficiency, cost-effectiveness, and sustainability. In this article, we will explore the many facets of prefabricated buildings, highlighting their benefits, processes, and how they are impacting the future of the construction industry.
What is Prefabricated Building?
Prefabricated building refers to the construction of structures or building components in a factory setting, where they are produced as individual parts before being transported to the construction site for assembly. This technique stands in contrast to traditional building methods that typically involve on-site construction from foundational materials. Prefabricated buildings can range from entire homes to commercial properties, and even bridges.
The Rise of Prefabrication in the Construction Industry
The growing popularity of prefabricated building is driven by several factors:
- Cost Efficiency: Prefabrication can significantly reduce labor costs and construction time, leading to lower expenses overall.
- Quality Control: Components are built in a controlled environment, making it easier to adhere to strict quality standards.
- Sustainability: Reducing waste and making efficient use of materials helps minimize the environmental impact of construction.
- Speed: The reduced construction time results in faster project delivery, which can be critical for businesses needing to meet deadlines.
Key Benefits of Prefabricated Buildings
Adopting prefabricated building solutions presents numerous advantages for contractors, architects, and property developers.
1. Quick Assembly Times
One of the most compelling advantages of prefabricated buildings is the speed of construction. Because many components are built simultaneously in a factory, the on-site assembly can be completed in a fraction of the time compared to traditional methods. This rapid turnaround not only saves time but also allows businesses to start generating revenue from their properties sooner.
2. Enhanced Quality Control
Factory settings allow for greater precision and quality in the production of building components. Automated processes and strict adherence to standards ensure that every unit meets high-quality requirements. This level of quality control can result in fewer defects and less need for on-site correction work, ultimately leading to higher customer satisfaction.
3. Reduction in Waste
Prefabrication significantly reduces materials waste. In traditional construction, about 20-30% of the materials can end up as waste. However, with prefabricated methods, this figure can be cut down drastically. Reusing materials and optimizing cutting plans further diminishes environmental impact, aligning with the growing demand for sustainable building practices.
4. Flexible Design Options
Many may assume prefabricated building is synonymous with limited design options; however, this could not be further from the truth. Advances in technology mean that custom designs and unique structures can be easily created using prefabricated elements. Modular designs can be combined, resized, or altered based on client needs, allowing for creativity and personalization in construction.
5. Improved Safety
Construction sites can be hazardous environments, but by manufacturing components in a controlled facility, safety risks are minimized. Less time on site and fewer workers are exposed to potentially dangerous conditions. Moreover, factory-built components have robust safety features integrated into their design, contributing to overall structural integrity.
The Process of Prefabricated Building
To understand how prefabricated buildings are made, it's essential to look at the overall process, which typically follows these stages:
1. Design and Planning
The first step involves detailed planning and architectural design. Contractors, architects, and clients collaborate to envision the final product, keeping in mind local regulations, aesthetics, and functionality.
2. Factory Production
Once designs are finalized, components such as walls, floors, and roofs are manufactured in a climate-controlled factory. This process includes the installation of essential parts such as plumbing, electrical wiring, and insulation during the initial manufacturing stage.
3. Quality Assurance
Each component undergoes rigorous quality checks to ensure they meet safety and structural standards. Any defects found can be addressed immediately in the factory, further enhancing the quality of the final product.
4. Transportation
After production, the components are safely transported to the construction site. Careful logistics are involved to ensure that everything arrives as planned and on schedule.
5. On-Site Assembly
The final stage is the assembly of the prefabricated building on-site. Experienced contractors execute the assembly process quickly and efficiently, ensuring that the building is structurally sound and ready for occupancy.
Prefabricated Building and Its Environmental Impact
As the world increasingly prioritizes sustainability, the role of prefabricated buildings becomes even more critical. Here are several ways that prefabricated buildings contribute to environmental conservation:
1. Energy Efficiency
Modern prefabricated buildings are designed with energy efficiency in mind. High-quality insulation and energy-efficient windows help keep heating and cooling costs down, resulting in smaller carbon footprints.
2. Sustainable Materials
Many prefabricated building companies focus on using sustainable materials, such as reclaimed or recycled products. This emphasis on eco-friendly materials helps reduce the consumption of new resources.
3. Reduced Transportation Emissions
By localizing manufacturing processes, transportation distances for materials and labor can be minimized. This reduction in transport not only lowers costs but also contributes to lower greenhouse gas emissions associated with transportation.
Challenges of Prefabricated Building
While prefabricated buildings offer numerous benefits, it is essential to acknowledge potential challenges. Overcoming these obstacles is crucial for broader acceptance in the construction industry.
1. Initial Cost Concerns
While the overall costs of prefabricated buildings can be lower, the initial investment for custom designs or specialized units may be higher than traditional methods. Educating clients on long-term savings is essential.
2. Perceptions and Misunderstandings
Some clients may have preconceived notions of prefabricated buildings being inferior or low-quality. This misconception must be addressed through education and high-quality marketing efforts.
3. Regulatory Hurdles
Prefabricated construction often faces strict local building codes and regulations. Navigating these legalities can be complex and may slow down the adoption of prefabrication methods.
The Future of Prefabricated Building
The outlook for prefabricated building is incredibly promising. As technology continues to evolve, the construction industry is likely to see several significant advancements:
- Smart Technologies: Incorporation of IoT (Internet of Things) devices and smart technologies will enhance the functionality and efficiency of prefabricated buildings.
- Greater Customization: Future advancements may allow for even more personalization options during manufacturing, catering to diverse client needs and preferences.
- Expansion into Emerging Markets: With developing countries facing pressing infrastructure needs, prefabricated solutions may provide rapid, scalable, and cost-effective alternatives.
Conclusion
In conclusion, the prefabricated building sector represents a transformative shift in construction methodologies that promises to enhance efficiency, quality, and sustainability. By embracing prefabrication, contractors and businesses in the construction industry can not only thrive but also play a crucial role in shaping a sustainable future. With the growing emphasis on environmentally-friendly practices, the demand for prefabricated solutions is set to rise, making it an excellent time for businesses to invest in this innovative approach.
For more information and resources on prefabricated buildings, visit module-t.com and discover how you can be part of the construction revolution.